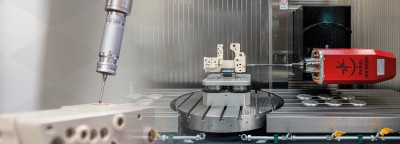
BKB Precision: 'We begin where 3D printing ends!
"BKB Precision: we begin where 3D printing ends!"
A statement made tongue-in-cheek, along with our explanation in this text.
3D printing with plastic is a booming business. Over the last ten years, its growth can be measured in double digits. But perhaps that’s not so surprising as 3D printing does meet an important need – it enables you to immediately see the tangible results of a design. That said, the ability to realise production from one single piece to series is an important factor in this growth. With all the developments taking place in 3D printing, completely new business models are emerging.
3D printing
This technology enables designers to create increasingly complex designs. However, 3D printing does have its limitations. For example, it is not yet possible to get the necessary tolerances and roughness with product manufacture as with current machining technology.
The current state of commercial 3D printing techniques suggest that the latest machines can produce parts in the tolerance class of maximum iT-13 (for dimensions between 20-80 mm).
Important factors when looking to get the right results are the minimum wall thickness and the detail size. Detail size is comparable to pixel size with cameras, albeit in 3D, but depending on which technique you use, it measures around 0.3 to 0.5 mm. The minimum wall thickness is about 1-2mm, which is often 3-4 times the detail size.
Because materials are often specifically designed for the 3D printing process, the properties of those materials need to be taken into careful consideration. At present, most high-tech plastics are either not suitable for 3D printing or they deviate from the ISO specifications on drawings. This has to do with the narrow melting area, which prevents the structure from becoming sufficiently homogeneous. Significant reductions in material properties such as strength and stiffness have to be taken into account.
Investments in new simultaneous processing techiques
BKB Precision will continue to monitor the state of 3D printing technology and if opportunities arise which benefit our customers (correct materials and tolerances), this will probably lead to investment. At present, this is not the case and there are still many advantages to conventional processing techniques.
We are trying to narrow the gap between editing and printing by improving our knowledge and skills, but also by investing in new simultaneous processing techniques (machines and software). When it comes to tolerances – assuming milling and turning in tolerance class iT 6-10 depending on material and product size – we calculate them at an average of ± 0.025mm.
We have had many customers begin with a design made by a 3D printer who then eventually came to BKB Precision to ask if we could also mill the object they made. The most common reasons for this have already been given above. These customers were often surprised when they discovered that machining had more design freedom than they thought.
In summary, 3D printing does have its own place in the industry, alongside machining and injection moulding, but it also makes the value of conventional plastics machining even more transparent. To illustrate this, here are some practical examples with their specific characteristics:
Investeren in nieuwe simultane bewerkingstechnieken
BKB Precision blijft de stand van de 3D-printtechniek op de voet volgen en als er mogelijkheden ontstaan die bij onze klanten passen (juiste materialen en toleranties) dan zal dat allicht tot investeringen leiden. Op dit moment is dit nog niet het geval en zijn er nog veel voordelen te halen met conventionele bewerkingstechnieken. We proberen de ‘gap’ tussen bewerken en printen steeds meer te verkleinen.
Onder meer door het verbeteren van onze kennis en kunde, maar ook door te investeren in nieuwe simultane bewerkingstechnieken (machines en software). Qua toleranties moet men bij frezen en kunststof draaien denken aan iT-klasse 6-10 afhankelijk van het materiaal en formaat van het product, gemiddeld rekenen wij met ± 0.025mm.
Meer designvrijheid bij verspanen
Er zijn vele voorbeelden van klanten die gestart zijn met een ontwerp in 3D-print en dan uiteindelijk bij BKB Precision komen om te vragen of wij dit ook kunnen frezen. De meest voorkomende redenen zijn hierboven al gegeven.
Men is dan ook erg verbaasd als blijkt dat verspanen uiteindelijk vaak meer designvrijheid heeft dan men dacht. Kortom, 3D-printen neemt haar eigen plek in binnen de industrie naast verspanen en spuitgieten en maakt de positie van het verspanen van kunststoffen alleen maar transparanter.
Ter illustratie van het voorgaande volgen hierbij een aantal praktijkcases met hun specifieke kenmerken.
Manifold
The design of a manifold (also called control blocks or valve blocks) has very diverse requirements. It must be lightweight, enable high flow, be chemical resistant, and have wall thicknesses of at least 1 mm, roughness of Ra 1.6 µm, and precision of up to 20 µm.
All this led to the design of a product to be made from PEEK. PEEK allows for small-scale wall thicknesses and has the correct chemical resistance. The precision requirements were also an important factor when choosing this material.
The high flow is achieved by rounding the channels at the intersections to keep resistance minimal. A great deal of cooperation between the designer and the manufacturer was necessary in achieving an optimal product.
Catheter
We produced a two-part catheter 17mm long and 2.2mm in diameter for a medical start-up. The requirements in advance: medical product to be used internally, very small (smallest detail 0.3 mm), high tolerances because the two parts must fit together perfectly, and the whole also had to be sterilisable. The biggest challenge was the level of detail – the smallest cutter used was 0.2mm!
By once more opting for PEEK, albeit this time a medical variant with accompanying certificates, it was possible to realise those details. A positive side effect of PEEK plastic is also its high temperature resistance of 260 °C, which is necessary if it is to be sterilisable.
Would you like to know more about BKB Precision, plastic processing or the techniques we use? You can contact us directly by calling +31 (0) 40 267 01 01 or send an email to info@bkbprecision.com.