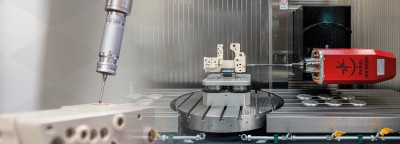
5 advantages of (technical) plastics for high-tech applications
Plastic is highly suitable as a material for high-quality and leading high-tech applications. We see an increasing demand for technical and high-performance plastics for medical applications, aerospace engineering, semicon, the automotive industry, electronics, and optical and precision instruments.
The reasons why plastic is chosen are different depending on the sector and application, but there are a number of advantages which apply to almost all of them. In this article, we list the 5 most common advantages of plastics for high-tech applications.
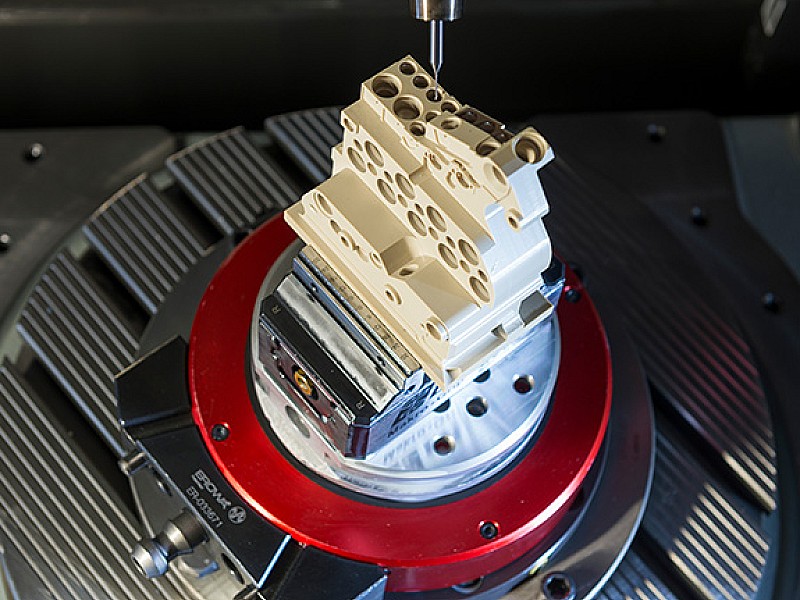
1. Lightweight
One of the biggest advantages of plastic over other materials such as metal is its low weight. This makes it possible for manufacturers to make their products even more energy-efficient, sustainable, useful, and environmentally friendly. Being made at the lowest possible weight can be a precondition for vehicle or aviation parts, housings, packaging materials, tank components, or medical devices. Machines which have housings made of plastic are easier to handle and transport.
2. Maximal strength of high-performance plastics
Different high-performance plastics have been developed to ensure excellent performance under extreme conditions. One example is PEEK, a very strong type of plastic with excellent tensile and flexural durability under varying loads and temperatures. Like PEEK, polyetherimide – or PEI – is one of the high-performance plastics. This type of plastic is widely used for aircraft components, partly because of its high mechanical strength. PAI (Polyamide-imide) also has excellent mechanical properties and is used for manufacturing parts which might be subjected to heavy loads.
3. Ideal for high precision machining
With the right expertise and advanced machinery, high-quality technical plastics can be processed very precisely. This makes plastic highly suitable for the manufacture of applications such as precision instruments. We do this by means of 3-axis milling, 4-axis milling or 5-axis simultaneous milling, a process in which all machining axes can be controlled simultaneously. At BKB Precision, we have 6 machines in our machine park in a climate-controlled environment, including robots. These machines make it possible to keep production going 24/7.
In addition, we specialise in:
- CNC turning
- CNC machining
- Plastic assembly
- Plastic cleaning
- Polishing or sanding
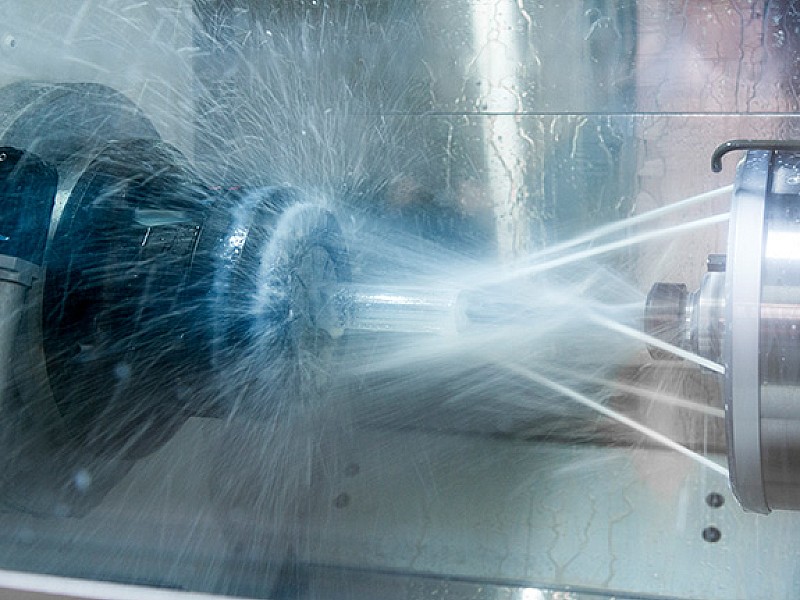
4. Long lifespan for technical plastics
Technical plastics have a longer lifespan than traditional materials. That makes these plastics highly suitable for applications where reliability and safety are of paramount importance. Examples include protective tubes for electricity and telecom cables, sewage systems, gas and water pipes, but also laboratory components and machine parts for the food industry.
Above all, a long lifespan results in lower maintenance costs, which means that increasingly more companies at home and abroad are looking to BKB Precision for the manufacture of high-quality plastic components for various high-tech applications.
5. Resistance to external influences
In many high-tech sectors, it is essential that the materials used are resistant to high temperatures, chemicals, and radiation. These are properties which can be found in various technical and high-performance plastics. We are happy to advise our customers on the right type of plastic to use for specific high-tech purposes.
Thanks to our expertise and years of experience in various market segments, we know exactly which engineering plastics are best suited for the desired purposes and outcomes.
We not only look at chemical and temperature resistance, but also at weight, dimensional stability, maximum strength, resistance to wear-and-tear, hydrolysis resistance, and, last but not least, processing options.
.