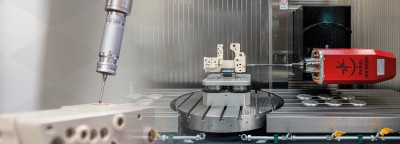
Why metal is increasingly giving way to plastic: a silent revolution in manufacturing
What if the material you have used for years is no longer the most logical choice? Metal has long been the standard in technical applications across many sectors, but behind the scenes plastic has gained significant ground in recent years. What are the advantages of plastics? Is this a structural shift? And what should you know before making the switch?
The history and rise of plastics
Metal was the undisputed standard in manufacturing for decades, yet that certainty is now under pressure. Plastics have made an impressive advance in recent years as an alternative. Whereas they were once primarily used as cheap substitutes for everyday applications, we now have access to a wide range of technical and high‑performance plastics.
Thanks to new production methods and growing insights into material properties, engineers are increasingly using plastics for demanding applications. Particularly in precision sectors such as semicon and analytical industries, where tolerances are minimal, plastic increasingly proves to be a smarter and better alternative to metal.
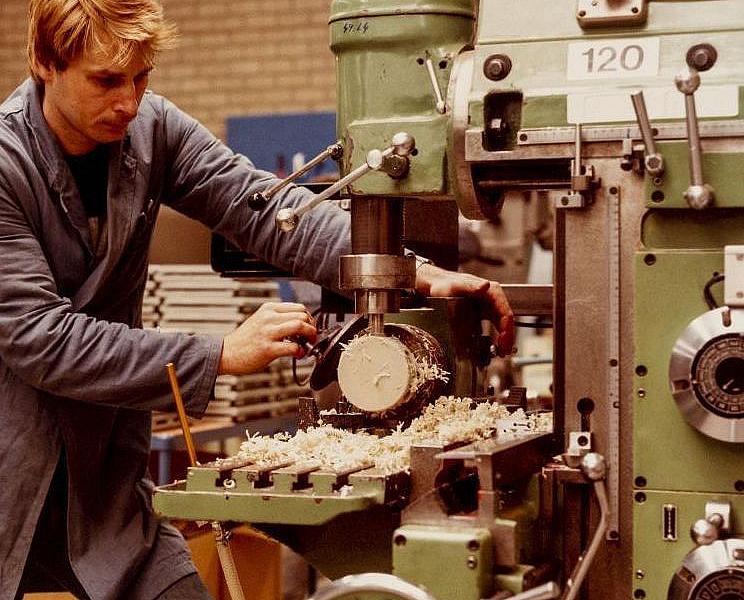
The advantages of plastic over metal
The choice for plastic is increasingly based on technical and economic considerations rather than assumptions. The advantages speak for themselves:
- Lighter weight without loss of strength
- Corrosion resistant and low maintenance
- High dimensional stability for precision machining
- Low coefficient of friction
- Saves costs on material, transport and production
With the wide variety of plastics available today, there is always a type of plastic that fits your application.
From metal to plastic: how that looks in practice
The difference is sometimes in the details. A customer from the semicon sector faced a choice: continue working with metal or take the step to plastic. Together with BKB Precision they explored the possibilities. By smartly redesigning the component in plastic, it became over half a kilo lighter per item. That saving translated into lower material costs, reduced transport weight, and a more stable process.
BKB Precision was involved from the start of this transition project: from material advice and machining techniques to cleaning and assembly. With our knowledge and experience we were able to respond quickly and jointly arrive at an optimal final product.
We have since successfully supported multiple customers from the semicon, analytical and other industries in similar material transitions. Discover how the complete project progressed or contact us for more assistance with your project.
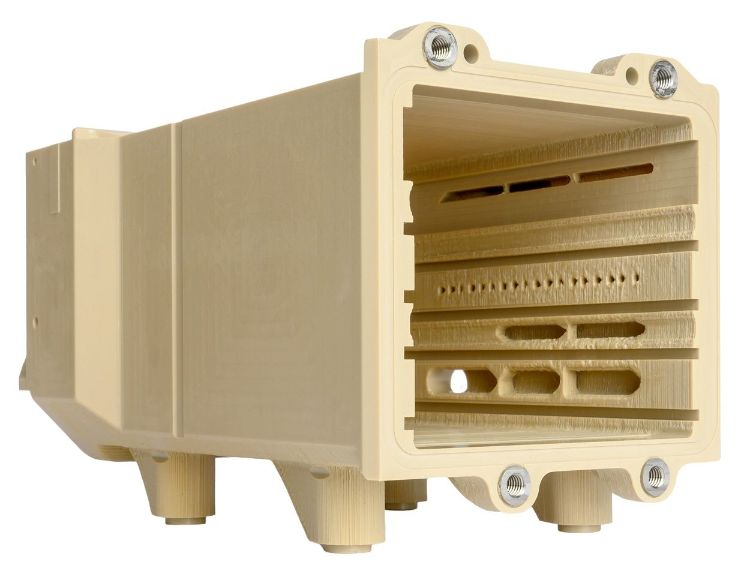
From metal to eco‑conscious: how plastic contributes to sustainability
In many applications plastic proves not only more practical, but also more sustainable than metal. It is lighter, corrosion‑resistant thus longer lasting, and requires less energy in production and use. Moreover, less mass also means lower emissions in transport, and reuse and recycling are increasingly feasible.
At BKB Precision we take our responsibility seriously. Every year we publish our progress on sustainability and continuously work to further green our processes and decisions. Discover our approach in our most recent sustainability report via the button below.
Future perspective: what can we expect?
The shift from metal to plastic is still in its infancy. But thanks to ongoing innovations in materials, more advanced machining techniques and growing expertise among engineers, the application possibilities for plastics will only increase. Think of lighter machines, smarter designs and more sustainable manufacturing processes.
At BKB Precision we push technical boundaries every day. We continually invest in knowledge, machinery and collaboration to maximize the potential of plastic machining, and we will continue to do so. What is groundbreaking today may become the new standard tomorrow.
Curious how we can support you with your next project?