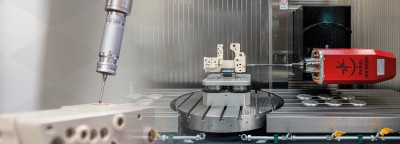
BKB Precision gaat door waar 3D-printen ophoudt
"Doorgaan waar 3D-printen ophoudt!"
Een stelling met een knipoog die wij graag van een toelichting voorzien.
Het 3D-printen in kunststof kent een enorme vlucht. De laatste tien jaar zelfs een groei met dubbele cijfers. Dat is ook niet zo verrassend omdat het in een grote behoefte voorziet, bijvoorbeeld om direct tastbaar resultaat te zien van een ontwerp. Maar ook het kunnen realiseren van enkelstuks tot en met serieproductie, was een belangrijke succesfactor voor deze groei. Met de ontwikkelingen rondom 3D-printen ontstaan er totaal nieuwe businessmodellen.
3D printen
Door deze techniek zijn ontwerpers in staat steeds complexere ontwerpen te maken. Echter kent 3D-printen ook haar grenzen. Zo is het verkrijgen van de juiste toleranties en ruwheden nog niet op het niveau van de huidige verspaningstechnologie.
De stand van de techniek van het commercieel 3D-printen geeft aan dat de nieuwste machines onderdelen kunnen produceren in de tolerantieklasse van maximaal iT-13 (voor afmetingen tussen 20-80 mm).
Belangrijk voor een goed resultaat zijn de minimale wanddikte en de detailgrootte. Detailgrootte bij 3D-printen, wat je zou kunnen vergelijken met een soort pixel grootte bij camera’s, zit, afhankelijk van welke techniek men kiest, rond de 0.3 tot 0,5 mm. De minimale wanddikte is ongeveer 1-2mm, dit is vaak 3-4 keer de detailgrootte.
3D printen en kunststoffen
Doordat men bij 3D-printen vaak specifiek voor het proces ontworpen materialen gebruikt, is ook qua materiaaleigenschappen enige voorzichtigheid geboden. Op dit moment zijn de meeste high-tech kunststoffen niet beschikbaar voor 3D-printen, dan wel wijken af van de ISO specificaties op tekeningen.
Dit heeft te maken met het smal smeltgebied waardoor de structuur niet voldoende homogeen kan worden. Er zal rekening gehouden moeten worden met significante vermindering van de materiaaleigenschappen, bijvoorbeeld sterkte en stijfheid.
Investeren in nieuwe simultane bewerkingstechnieken
BKB Precision blijft de stand van de 3D-printtechniek op de voet volgen en als er mogelijkheden ontstaan die bij onze klanten passen (juiste materialen en toleranties) dan zal dat allicht tot investeringen leiden. Op dit moment is dit nog niet het geval en zijn er nog veel voordelen te halen met conventionele bewerkingstechnieken. We proberen de ‘gap’ tussen bewerken en printen steeds meer te verkleinen.
Onder meer door het verbeteren van onze kennis en kunde, maar ook door te investeren in nieuwe simultane bewerkingstechnieken (machines en software). Qua toleranties moet men bij frezen en kunststof draaien denken aan iT-klasse 6-10 afhankelijk van het materiaal en formaat van het product, gemiddeld rekenen wij met ± 0.025mm.
Meer designvrijheid bij verspanen
Er zijn vele voorbeelden van klanten die gestart zijn met een ontwerp in 3D-print en dan uiteindelijk bij BKB Precision komen om te vragen of wij dit ook kunnen frezen. De meest voorkomende redenen zijn hierboven al gegeven.
Men is dan ook erg verbaasd als blijkt dat verspanen uiteindelijk vaak meer designvrijheid heeft dan men dacht. Kortom, 3D-printen neemt haar eigen plek in binnen de industrie naast verspanen en spuitgieten en maakt de positie van het verspanen van kunststoffen alleen maar transparanter.
Ter illustratie van het voorgaande volgen hierbij een aantal praktijkcases met hun specifieke kenmerken.
Manifold
Het ontwerpen van een manifold (ook wel besturingsblokken, ventielblokken of verdeelstukken genoemd) heeft in dit geval zeer diverse eisen: licht van gewicht, hoge flow, chemisch resistent, wanddiktes van minimaal 1mm, ruwheden Ra 1,6µm en nauwkeurigheden tot 20µm.
Dit heeft ertoe geleid het ontworpen product uit PEEK te maken. PEEK staat geringe wanddiktes toe en heeft de juiste chemische resistentie. Ook de nauwkeurigheidseisen waren hier een belangrijke factor voor deze materiaalkeuze.
De hoge flow is gerealiseerd door de kanalen op de kruispunten dusdanig af te ronden teneinde de weerstand zo minimaal mogelijk te houden. Hier is veel samenwerking tussen ontwerper en maker noodzakelijk om tot een optimaal product te komen.
Katheter
Voor een medische startup is een katheter geproduceerd van 17mm lang en 2,2mm diameter, dat is opgebouwd uit twee delen. De eisen vooraf waren: medisch product dat inwendig gebruik wordt, zeer klein (kleinste detail 0,3mm), hoge toleranties omdat de twee delen perfect op elkaar moeten aansluiten en het geheel moest ook steriliseerbaar zijn. De grootste uitdaging was het detailniveau, de kleinste frees die hierbij gebruikt is, was 0,2mm!
Door wederom te kiezen voor PEEK, maar nu voor de medische variant met bijbehorende certificaten, was het mogelijk om deze details te realiseren. Een mooie bijkomstigheid van PEEK kunststof is de hoge temperatuurbestendigheid van 260 °C, wat ook noodzakelijk is voor het steriliseren.
Wilt u meer weten over BKB Precision, kunststof bewerken of de technieken die wij hiervoor toepassen? Neem dan direct contact met ons op.